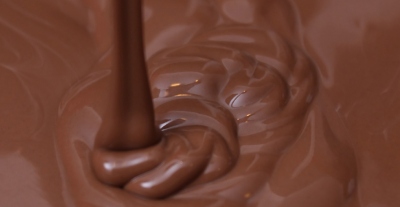

Recycling of multilayer and composite plastics

Plastics bring value as convenient, versatile and lightweight consumer products, as well as advanced performance in high-end applications such as automobiles. However, despite their usefulness, it is clear that linear, single-use consumption of plastics is incompatible with Europe’s transition to a circular economy. This model prioritises the reuse and recycling of resources, with the aim of reducing waste and retaining as much value as possible.
In terms of plastics recycling, some progress has been made. For example, 41.5% of the plastic packaging waste generated was recycled in 2018. This is still not enough to achieve full circularity, especially in the recycling of multilayer plastics that are difficult to separate. In addition, it is essential that recycling technologies keep up with new materials entering the market
Advanced plastics recycling
The EU-funded MultiCycle project aims to develop a pilot plant for industrial recycling and treatment of multilayer plastics. This plant focuses on two important industrial segments that pose a challenge for recyclers: multilayer packaging/flexible films and fibre-reinforced thermoplastic composites of the type used in the automotive sector.
Technology selection
NIR and HSI-NIR are the techniques conventionally used for container sorting. The former is suitable for individual pieces of packaging prior to shredding and can also provide an initial assessment of suitability before moving on to the latter, which provides a mode of imaging. In the MultiCycle project, packaging materials were fed onto a conveyor in the form of flakes up to 5 cm and therefore HSI was the target technique for final implementation in the prototype incoming control system. However, point NIR spectroscopy was the target technique used for monitoring dissolved and recovered plastics during and after the CreaSolv® process, where no imaging capability is required. Complementary techniques such as LIBS and FTIR have also been preliminarily tested to detect other fractions such as AlOx or to enable the detection of black containers, which could improve the accuracy of monitoring when a full system is implemented.
Near Infrared Spectroscopy (NIRS)
NIR spectroscopy is a vibrational spectroscopic technique. In this region, absorption spectra are composed of overtones and combination bands with respect to the fundamental modes of molecules in the mid-infrared region. NIR radiation has a wavelength range of 900 to 2500 nm. The absorption bands in this region are broad, due to the high degree of band overlap. In addition, due to the selection rules of the phenomena, the signal intensity is ten to a thousand times weaker than signals in the mid-infrared region. However, this lack of intensity and the high band overlap is compensated by its high specificity. The specificity of NIR spectroscopy is based on the fact that NH, OH and CH bonds strongly absorb radiation at these wavelengths, which makes it an optimal tool for the study of organic compounds and polymers. In addition, the use of multivariate methods for the analysis of spectral data has made it possible to exploit the full potential of the technique for identification, discrimination, classification and quantification purposes.
Hyperspectral imaging system in the shortwave infrared region (HSI-SWIR)
Current technologies for the monitoring and classification of solid plastic waste in the near-infrared region have incorporated hyperspectral cameras in their configuration. They allow, instead of collecting a single spectrum, to record a hyperspectral image (HSI) of the sample (hyperspectral cube), which contains not only the spatial location of the sample, but also its chemical composition and distribution. In this regard, several publications and technological developments have been made using HSI-SWIR for the classification and identification of plastics.
A basic hyperspectral imaging system, shown in Fig.3, includes in its configuration, a sensitive sensor (CCD camera); a broadband illumination source; a spectrometer, which separates the backscattered/transmitted light into its different wavelengths and, when required, a conveyor belt for sampling. In this case, it should be noted that the conveyor belt must be synchronised with the recording speed of the CCD sensor for proper image acquisition. A hyperspectral system provides a hypercube as output. A hypercube is a set of data arranged in three dimensions, two spatial (an XY plane) and one spectral (𝜆, wavelength), as depicted below.
Measurement parameters:
The most relevant parameters for hyperspectral cube recording can be summarised as follows:
- Camera frame rate (fps)
- Transporter speed (m/s)
- Camera-transporter distance (cm) and collection time (µs). These parameters are interrelated and must be optimised to obtain good quality recorded spectra.
The hyperspectral images were recorded with a SWIR camera operating in the range ∼900-1700 nm, at a frame rate of 214 fps, with an integration time of 350𝜇s and a transporter speed of 25m/min.
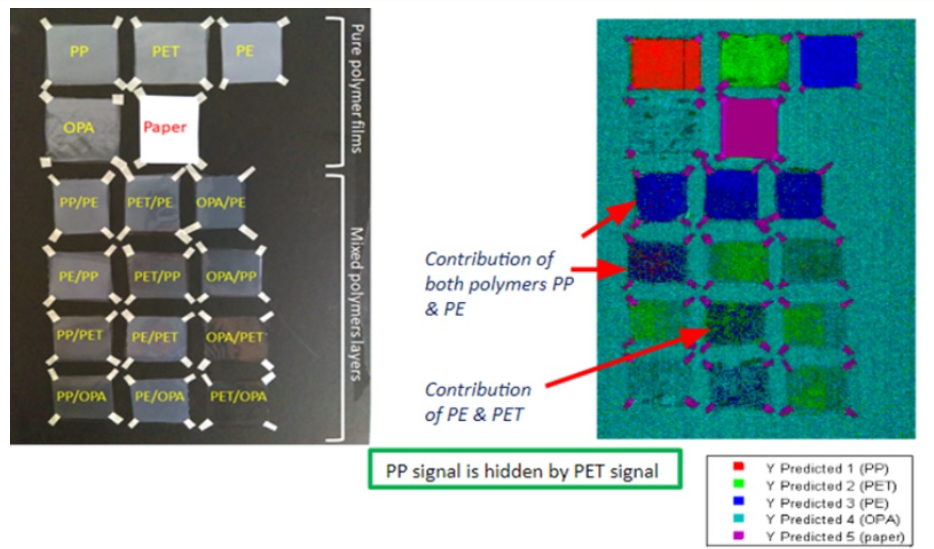
Figure 1: (Left) Sample set no. 1. Includes flexible plastic films of PE, PP, PA and PET. Single and double combinations of these polymers (i.e. polymer A/polymer B) were included. (Right) Classification image made by a PLSDA model.
Project conclusions
The HSI monitoring system has been able to provide a good approximation of the percentage of polymer content in a multilayer polymer sample. In the worst case, the most abundant polymer present in the sample is predicted, so with large batches, the final percentages would be fairly accurate. In terms of monitoring the dissolution process, only 1 polymer and 1 solvent were provided for testing in IRIS. The results obtained with Visum Palm™ were as expected, but no process models were tested over time. The dissolution control was not performed due to problems with the viscometer installed in LOEMI. For this reason, there are no further results in this section.
For the monitoring of the automotive samples, the selected technique was LIBS. The optimisation of LIBS was complicated, as it was the first time it was used. Models were run by changing different parameters to select the best conditions. The PATbox tool for LIBS did not allow data acquisition at the same speed as the LIBS software, so the models had to be modified. Finally, the models were calibrated and tested to predict the type of fibres in the black plastics PP and PA. The results obtained in the 3 batches were satisfactory, as the predictions given by the models (chemometrics and machine learning) were close to the real content. Some tests were performed to differentiate between PP and PA, but the classification rate was around 80% of good predictions. In general, mislabelling and soiling of the samples were not very useful for the development of the prediction models.