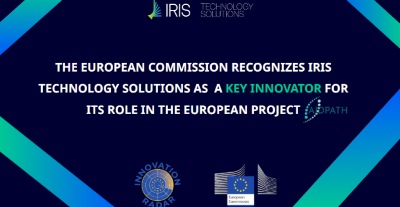
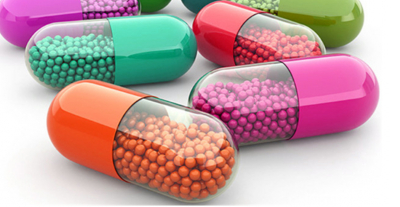
Surveillance du processus de mélange par spectroscopie NIR en ligne
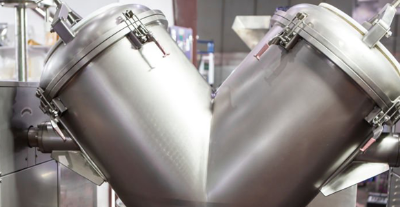
Surveillance du processus de mélange en temps réel par spectroscopie NIR
Le processus de mélange de poudres est le plus répandu pour obtenir une uniformité de contenu dans les formes solides. Malgré son apparente simplicité, à savoir tirer parti des forces de cisaillement pour mélanger les principes actifs et les excipients en déplaçant simplement le récipient pendant un certain temps, tout spécialiste de la galénique sait que le comportement réel du mélange n’est pas aussi simple. En fait, la distribution finale résulte d’une combinaison chaotique d’interactions microscopiques entre les particules et de la mécanique macroscopique des flux, sans compter qu’une fois l’homogénéité atteinte, il existe un risque réel de démixtion en raison de l’affinité entre les particules homologues. C’est pourquoi, quelles que soient les améliorations mécaniques apportées à la conception du mélangeur, le contrôle systématique de l’homogénéité du mélange est une exigence essentielle dans le secteur pharmaceutique et nutraceutique. C’est là que la spectroscopie NIR prend toute son importance en tant que technique de surveillance du processus de mélange en temps réel.
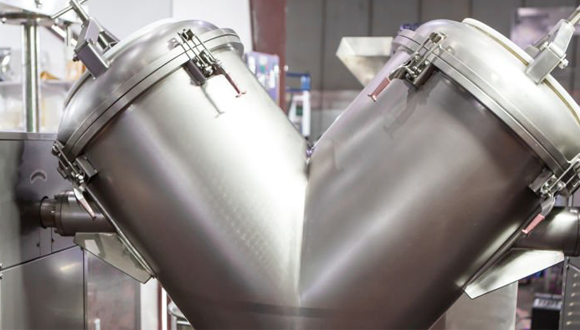
Contrôle traditionnel du processus de mélange par rapport au surveillance du processus de mélange (PAT)
Jusqu’à présent, la méthode traditionnelle consistait à arrêter périodiquement le processus de mélange après plusieurs cycles afin de prélever des échantillons en différents points, qui sont ensuite analysés par chromatographie. Toutefois, cette approche présente également certains inconvénients indésirables, à savoir un délai supplémentaire (en raison de la lourdeur des procédures de laboratoire), un temps de mélange sous-optimal (en raison d’un mélange prolongé arbitraire destiné à garantir l’homogénéité) et des artefacts de mélange (tels que le démélange et les grumeaux, conséquence du maintien de la charge dans des conditions statiques en attendant les résultats du laboratoire).
Au contraire, une approche PAT, telle que la surveillance du processus de mélange en temps réel par spectroscopie NIR, pourrait être considérée comme le meilleur moyen de vérifier si le critère d’évaluation a été atteint. En fait, la FDA et l’EMA ont toutes deux décrit cette approche comme un nouveau paradigme recommandé.
En principe, comme le décrit en détail la littérature scientifique, il existe deux façons de mettre en œuvre une détermination du point final basée sur la PAT : en utilisant un modèle prédictif de machine learning supervisé (par exemple, un modèle PLS qui prédit quantitativement la concentration de l’API) ou en utilisant un algorithme qui ne tient pas compte de la composition spécifique du mélange. La première solution donne généralement des résultats plus directs et plus précis, mais elle nécessite le développement de modèles spécifiques sur la base d’échantillons de référence appropriés, ce qui n’est pas toujours possible, en particulier lorsqu’il existe un trop grand nombre de formulations différentes. L’approche agnostique pour la surveillance du processus de mélange, au contraire, est basée sur la similarité spectrale ; aucune donnée de base sur la composition spécifique de chaque formulation n’est requise à l’avance.
L'approche agnostique : L'écart type à blocs mobiles et l'algorithme dynamique par IRIS Technology Solutions
La stabilité spectrale est, en fait, indépendante de la composition spécifique de chaque formulation. Il n’est pas nécessaire de développer un modèle prédictif quantitatif pour évaluer les concentrations des composants, car le raisonnement sous-jacent stipule que, quelle que soit la composition, aucune amélioration de l’homogénéité ne peut être apportée dès lors que les spectres restent inchangés, du moins pour les principaux composants. En effet, un mélange peut être considéré comme homogène lorsque leurs spectres restent inchangés après plusieurs cycles de mélange.
Étant donné que la spectroscopie NIR est sensible à des concentrations de 0,1-1 % ou plus, il n’est pas possible d’évaluer l’homogénéité des composants mineurs au moyen d’une telle technologie pendant la surveillance du processus de mélange. Toutefois, elle peut être déduite de l’homogénéité des principaux composants et, le cas échéant, validée par des méthodes de laboratoire traditionnelles.
L’écart type des blocs mobiles (MBSD) est l’algorithme agnostique le plus largement décrit, du moins dans la littérature scientifique. En général, le critère d’évaluation de l’écart type des blocs mobiles est plutôt arbitraire. Même lorsqu’un critère statistiquement fondé est utilisé [Critical evaluation of methods for end-point determination in pharmaceutical blending processes. M. Blanco, R. Cueva-Mestanza et J. Cruz. Anal. Methods, 2012, 4, 2694], certaines hypothèses restrictives sur la distribution de la métrique de similarité doivent être remplies pour être correctement applicables. En outre, la moyenne de l’écart type a un effet plutôt « lissant » qui pourrait voiler dans une certaine mesure la tendance réelle de la similarité spectrale.
L'approche dynamique avec Visum NIR In-Line™ pour la surveillance des processus de mélange
L’algorithme propriétaire d’IRIS Technology Solutions, au contraire, est basé sur la vérification de la stabilité d’une véritable métrique de similarité (MSD : différence quadratique moyenne entre deux spectres successifs) en utilisant des critères statistiques forts sur la distribution MSD spécifique au mélange. En fait, notre approche par blocs mobiles adapte dynamiquement le seuil à chaque distribution statistique de similarité spectrale propre à la formulation. Par conséquent, elle fournit un critère d’extrémité robuste pour la surveillance du processus de mélange indépendamment du comportement spécifique de chaque formulation, ce qui est particulièrement nécessaire lorsque des anomalies de mélange telles que le démélange ou la formation de grumeaux se produisent.
Par souci de flexibilité, les utilisateurs peuvent régler à leur convenance la taille du bloc mobile et la signification statistique. Dans la mesure du possible, ces paramètres doivent être réglés lors de la phase de mise en service, bien que les valeurs réglées en usine soient suffisantes pour les cas les plus fréquents.
Image 1 : Module adaptateur de fenêtre en saphir pour l’analyseur en ligne Visum NIR ™ fabriqué par IRIS Technology Solutions S.L.
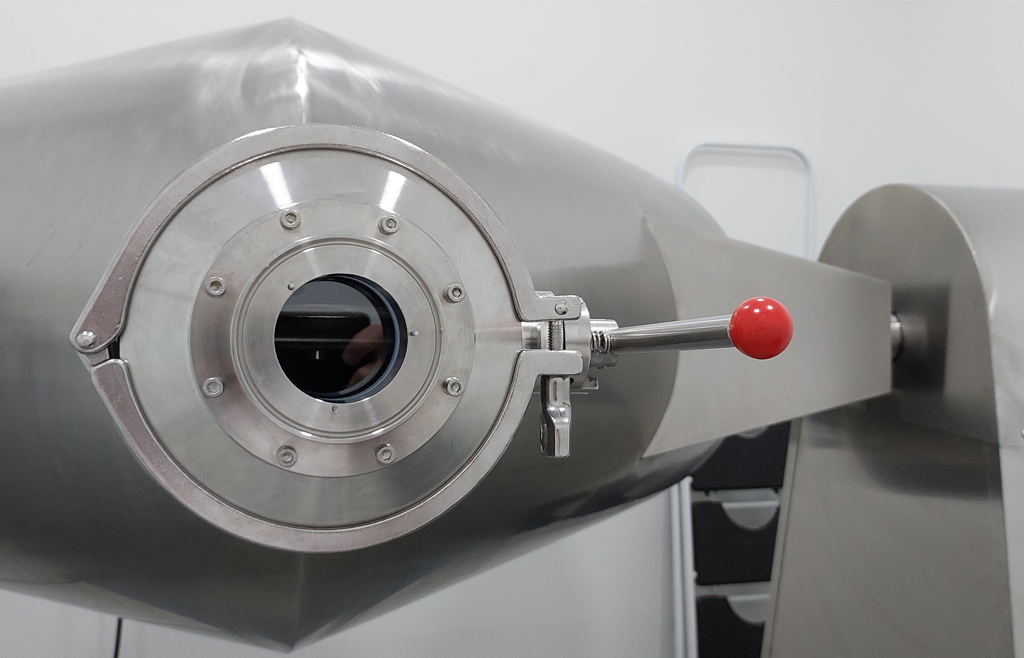
Le module adaptateur avec fenêtre en saphir permet d’intégrer facilement l’analyseur Visum NIR In-Line™ via une connexion tri clamp. Il existe différentes tailles de module adaptateur en fonction des configurations propres au mélangeur.
Contrairement aux autres analyseurs du marché, le Visum NIR In-Line™ est un analyseur autonome (ordinateur embarqué) et peut communiquer avec plusieurs protocoles de communication. Il est également conforme à la réglementation pharmaceutique 21 CFR Part 11 (FDA), aux exigences des pharmacopées américaine (USP) et européenne (Ph. Eur.) et aux lignes directrices 2014 et 2023 de l’Agence européenne des médicaments (EMA).
Dans sa version Blender, l’analyseur Visum NIR In-Line™ est sans fil, alimenté par des batteries rechargeables et remplaçables d’une autonomie de plus de 3 heures et connecté par Wi-Fi, comme le montre l’image ci-dessous.
Image 2 : L’analyseur Visum NIR In-Line™ dans un cycle de surveillance du processus de mélange.
Tableau 1 : Caractéristiques techniques de l’analyseur en ligne Visum NIR In-Line™
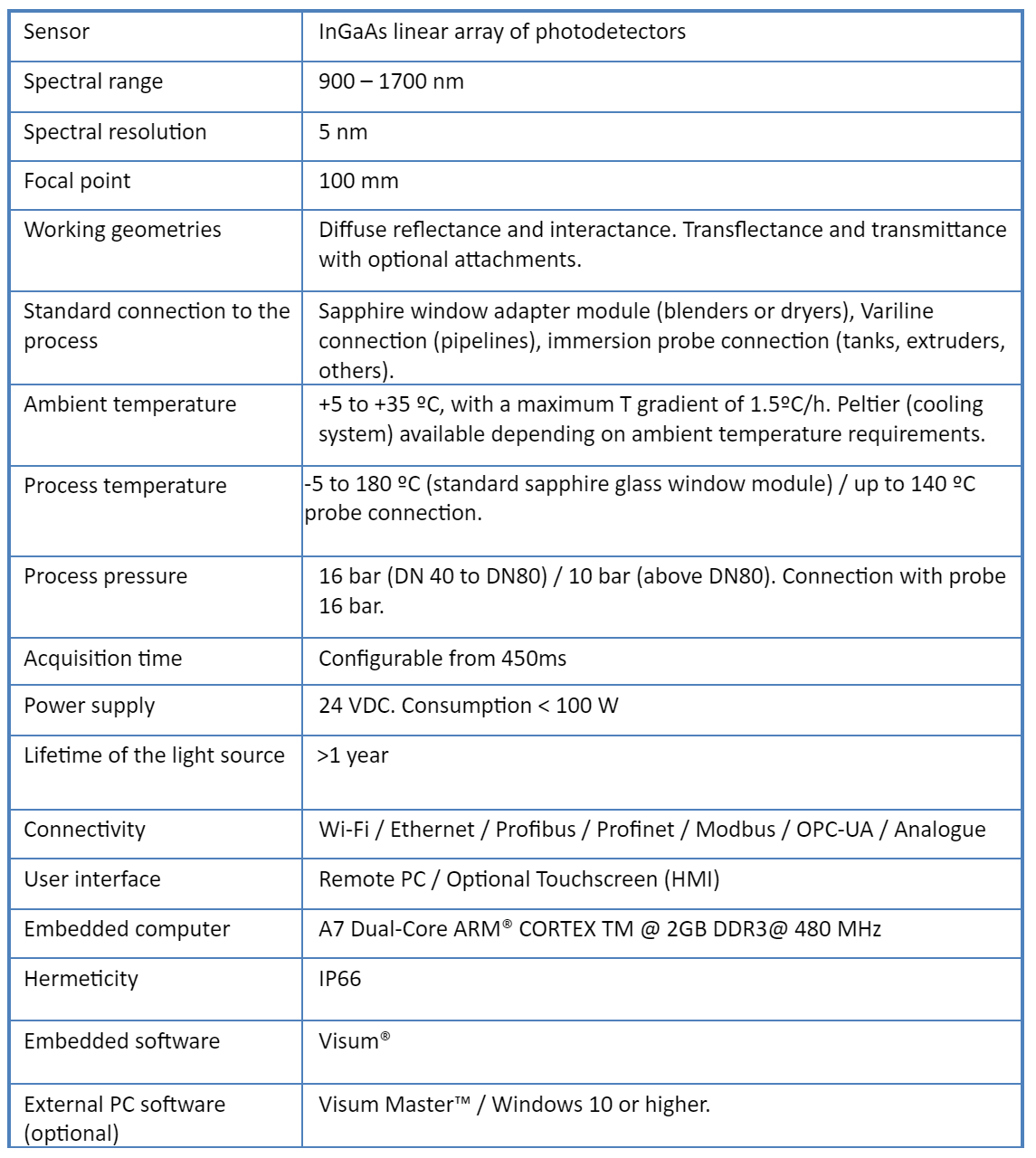
Conclusions
L’analyseur NIR In-Line™ d’IRIS Technology Solutions S.L. présente une méthode dynamique plus robuste et plus réaliste pour la surveillance du processus de mélange que l’algorithme Moving-block Standard Deviation (MBSD), car il est basé sur la moyenne quadratique de deux spectres successifs et non sur la moyenne de l’écart-type comme indice de similarité utilisé par l’approche MBSD.
Comme il est doté d’un ordinateur intégré, il n’a pas besoin d’être connecté à d’autres appareils électroniques ou à des ordinateurs externes, ce qui en fait un excellent outil autonome pour travailler au niveau de la production de l’usine et dans des environnements BPF.
En outre, il dispose d’une zone d’illumination et d’acquisition de spectre beaucoup plus grande que les autres analyseurs NIR, en particulier ceux de très petite taille, avec une résolution de 256 pixels, ce qui permet d’obtenir davantage d’informations chimiques et de qualité spectrale pour une surveillance optimale de chaque cycle de mélange.