
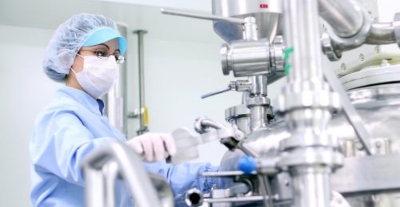
NIR in the Woodworking Industry: Particleboard Real-Time Quality Control

The wood industry, and in particular the manufacture of wood panels, has enormous advantages for the introduction of photonic techniques such as near infrared spectroscopy (NIRS) in the different phases of the production process that are currently controlled mechanically, randomly or simply escape from traditional control and manufacturing techniques.
IRIS Technology is the most important European supplier of advanced control systems with spectroscopy and artificial intelligence applied to production processes in different industries, including manufacturers of wood or particle boards. These boards consist of shavings of different sizes that form a multilayer structure and that, finally, may or may not be coated with decorative paper impregnated with melamine resin. Undoubtedly, particleboard has many applications in the furniture, furnishing, construction and interior finishing industries.
As a specialised supplier in the control of particleboard manufacturing, IRIS Technology has launched several applications in its Visum® line of analysers using hyperspectral technology, which we will tell you about below:
Chipping process
Wood chips make up the raw material in the manufacture of particleboard and can be of different kinds or origins. At the production line, IRIS Technology’s hyperspectral imaging system Visum HSI™ is able to determine in real time the proportion (quantification) of each class or type of chips, as well as to determine the average moisture content of the chips passing through the conveyor belt and to detect surface foreign bodies that are not controlled by X-rays such as rubber, plastics, or others of lower density.
As the raw material is mainly cut into chips in a wet state and according to the origin and type of wood there is variability in terms of moisture content, having accurate and objective information in real time is a useful tool to adjust the subsequent processes of defibration and drying.
Gluing – Urea formaldehyde content Quantification or Classification
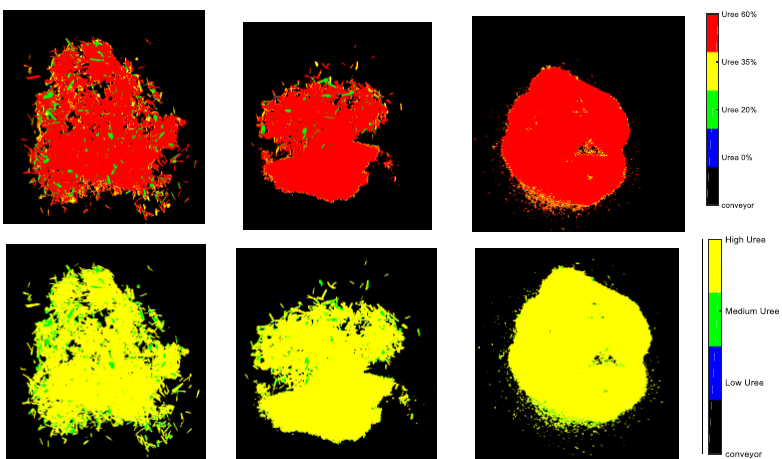
Numerous adhesives, binders or resins such as urea formaldehyde, among the most widespread for their enormous advantages in particleboard production, are applied in the gluing process. The mixture of the wood chips together with the adhesives determines the consistency and quality of the board resulting from pressing.
The Visum HSI™ analyzer allows real-time monitoring, classification, quantification and determination of the spatial distribution of this adhesive compound without the need for destructive or laboratory techniques and thus detects anomalies to optimize the gluing process or formulation.
Pressing and curing of boards
The pressing process is not a uniform process since to a large extent, the curing will depend on the variability that exists in the subsequent stages of the manufacturing process. Here at IRIS Technology, we find that the wood industry uses different scales to determine the quality of the curing of the boards and that it currently extends to a few samples produced per batch and destructive.
Also through IRIS hyperspectral systems, it is possible to observe and classify the curing factor of complete boards, unit by unit, obtaining chemical and spectral information of each pixel observed by the system, becoming a crucial instrument in the final quality control of the particle board.
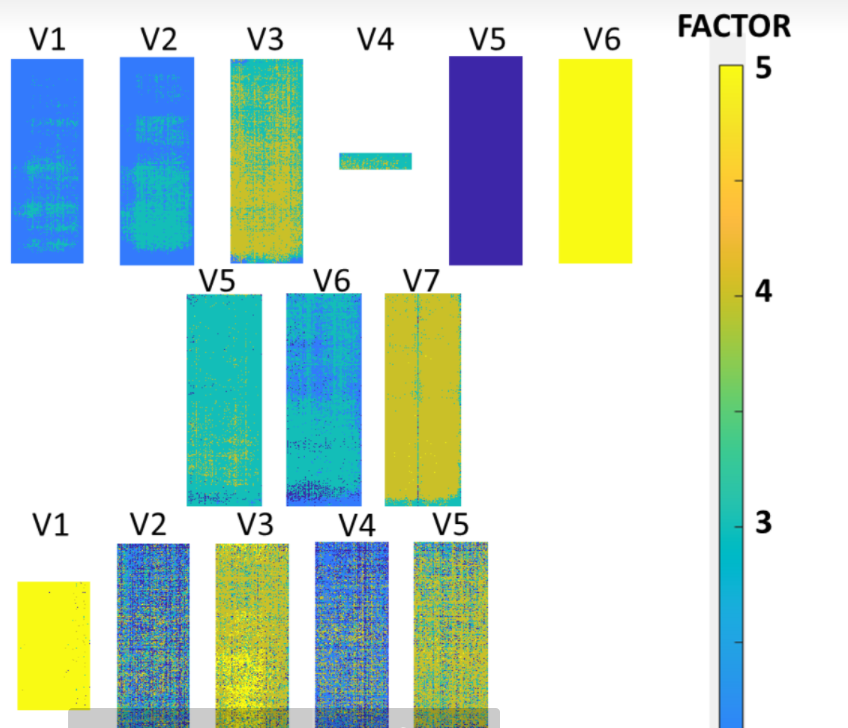
Impregnation – Moisture Control In-Line
Finally, impregnation is the process by which the paper layer that acts as a decorative coating for the particleboard is impregnated. Moisture is the main quality factor here, as it will ultimately affect the quality and durability of the impregnation. The hyperspectral systems imaging Visum HSI™ at this point is able to determine the homogeneity and quantify the moisture so as to be able to detect and correct deviations or anomalies that will result in losses, claims and returns.
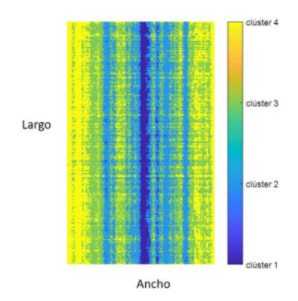
For further information about us and our hyperspectral systems, and applications please contact us at info@iris-eng.com.