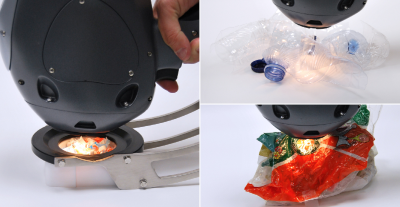
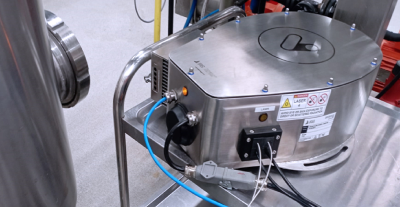
Real-time monitoring of free lacticide during the production of PLA (polylactic acid)
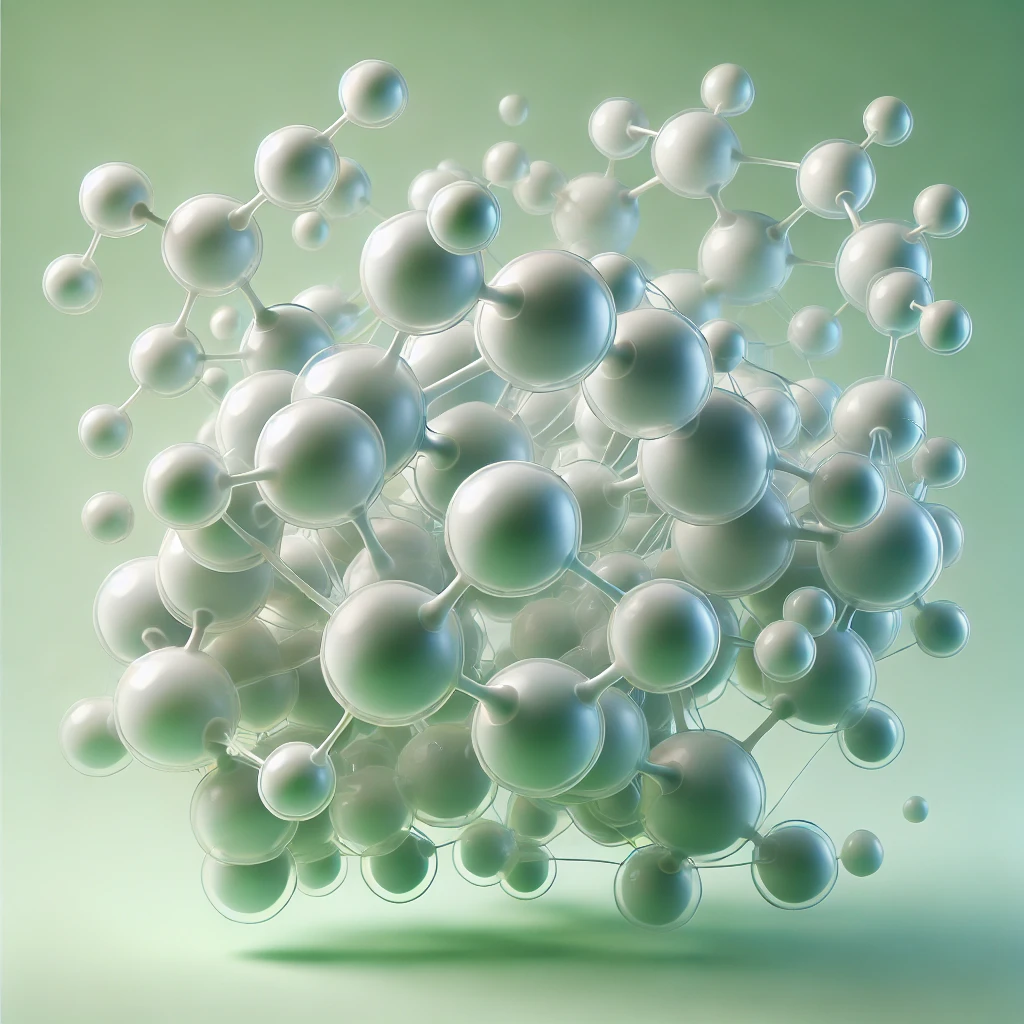
Monitoring of free lacticide levels during PLA (polylactic acid) production in real-time.
Reactive extrusion - REX
Reactive extrusion (REX) is a method of chemically modifying polymers during the extrusion process to improve their properties. Combining reaction and extrusion means taking advantage of the synergistic effects of shear forces and temperature to complete the reaction in less time, while the product is obtained directly in its final form.
One of the advantages of reactive extrusion is that the reactions are carried out without solvents or with a minimal amount compared to traditional batch polymerization processes. The result is a considerable reduction in costs and emissions, which makes the process more sustainable.
However, since each reactive extrusion process involves several characteristics, such as extruder geometry, screw speed, temperature profile, as well as the ratio and feed rate of the reactive species, which, in turn, are closely related to the throughput and residence time, the process is particularly complex and usually cannot be adequately modelled in terms of simple recipes or simple manufacturing rules.
Polylactic acid (PLA)
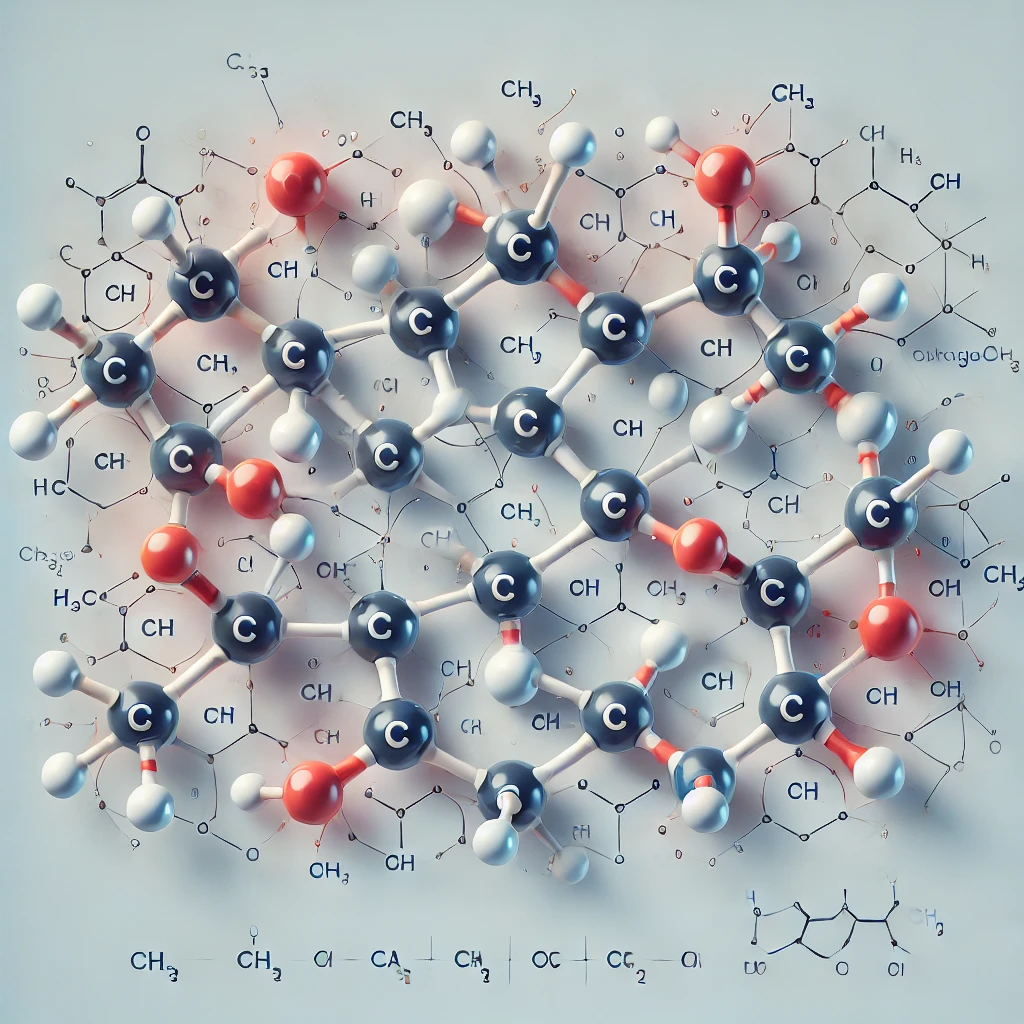
PLA structural unit
Polylactic acid is a monomer used for the synthesis of PLA and is a bioplastic, i.e. bio-based and biodegradable, obtained from the anaerobic fermentation of renewable food sources and has numerous applications in the compostable packaging industry, its use as a filament in 3D printing and in the medical or surgical industry. It is also a rigid thermoplastic that can be semi-crystalline or fully amorphous, depending on the purity of the stereoisomer.
Visum NIR In-Line Probe™ as a control tool to monitor PLA synthesis by reactive extrusion
The use of analytical tools based on NIR spectroscopy provides a source of real-time information about what happens inside the reactive extruder during the L-lactide Ring Opening Polymerisation (ROP) process.
In this case, the most important source of information is the amount of L-lactide that has not reacted or polymerised during the process. Both the purity and the yield in terms of molecular weights as well as the mechanical and thermal properties of the product are highly dependent on the efficiency of the process.
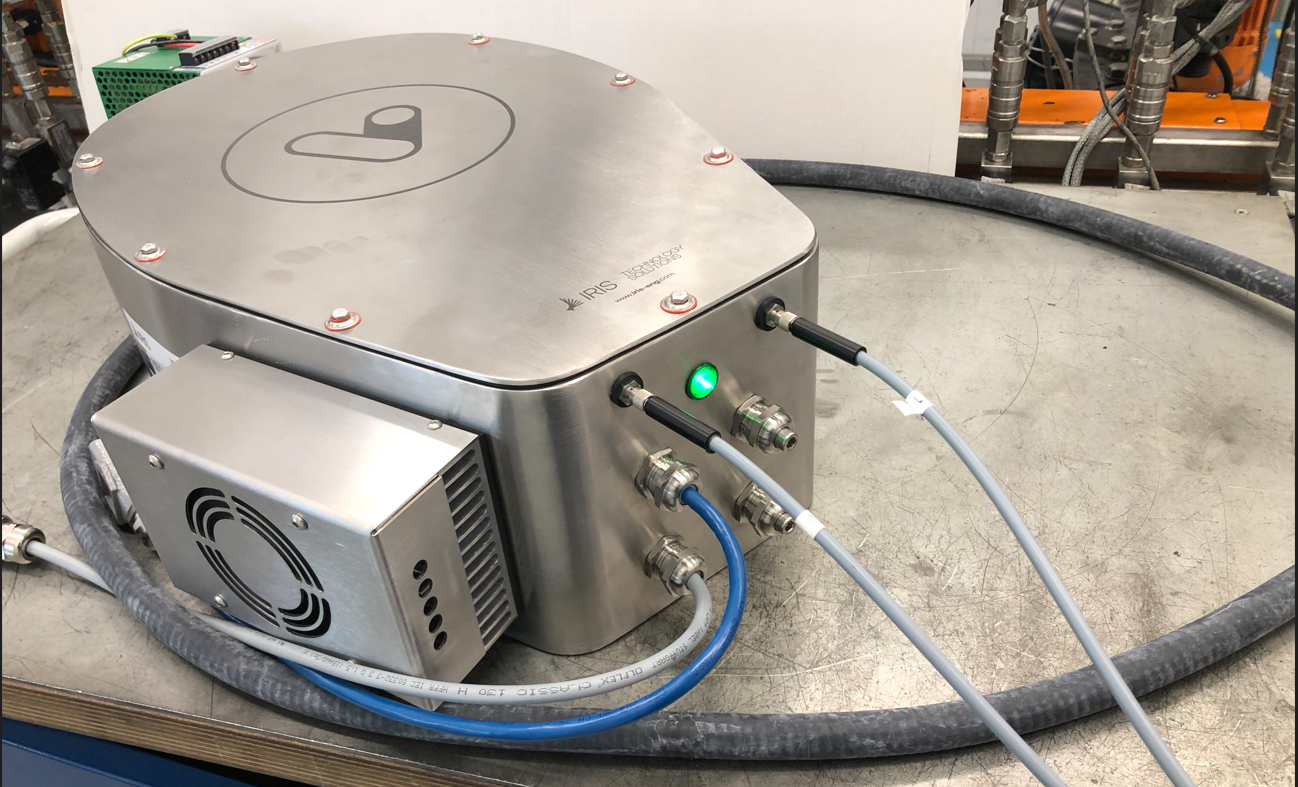
Visum NIR In-Line Probe™ monitoring PLA synthesis in ROP process
The process analyser Visum NIR In-Line Probe™ -designed, manufactured and marketed by IRIS Technology Solutions, S.L.- (Spain) has been successfully used to monitor the polycondensation reaction of lactic acid that normally takes place at temperatures above 180 °C.
Unlike its sibling Visum NIR In-Line™ analyser, the Probe version has been specifically designed to work in even more aggressive environments using transmittance, reflectance or transflectance optical probes depending on the characteristics of the matrix to be monitored and the particular process conditions such as temperature, viscosity, pressure and explosion risk.
To monitor the reaction, a reflectance probe was used, attached to a reactor port suitably machined for this purpose.
As can be seen below, the predicted lactide concentration values have an RMSEP of 1.6% w/w when compared to the reference laboratory analysis, which is a more than acceptable uncertainty because the typical amount of lactide remaining is between 5 and 10%. The alternative, off-line analysis by chromatography (HPLC) could involve a waiting time of about 1 day, which is not suitable for any efficient process control task.
The ultimate goal is to optimise the residence time in the reactor: the shorter the better, as long as the concentration of remaining lactide (which has not polymerised) is kept low enough to guarantee the quality and purity of the final product. Incorrect extrusion settings result in loss of time, energy and raw materials, as the process is not reversible.
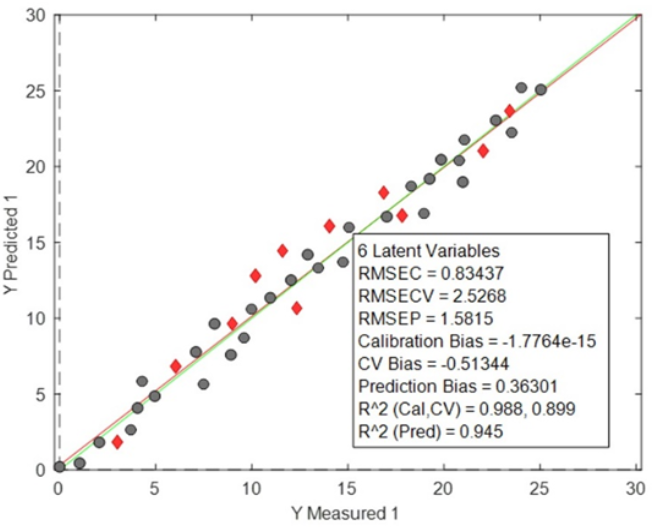
Machine learning predictive model metrics and regression lines. Grey dots represent modelling (“training”) spectra, while red dots represent validation spectra, which have not been included in the training set. Ordinates: Predicted L-lactide concentrations. Abscissae: Reference L-lactide concentrations provided by the traditional (HPLC) method.
In relation to the machine learning model, using the Model Builder of the proprietary Visum Master™ software, a non-expert user can easily create tailor-made calibrations as long as some reference spectra and the respective analyte concentrations are available. Since the Model Builder works according to AI heuristics, the best combination of mathematical pre-treatments and machine learning algorithms is found automatically without any input from the user. This means that the user could extend the applicability of the online analyser to a wider range of future applications beyond the specific case of PLA manufacturing.
In summary, since the Visum NIR In-Line Probe™ analyzer can acquire and mathematically process a representative spectrum in a fraction of a second, the entire reactive extrusion process can be automatically inspected in terms of the remaining amount of L-lactide so that the user can make real-time decisions on the updated optimal parameters.